Top Pitfalls to Avoid with Pedestrian Lighting
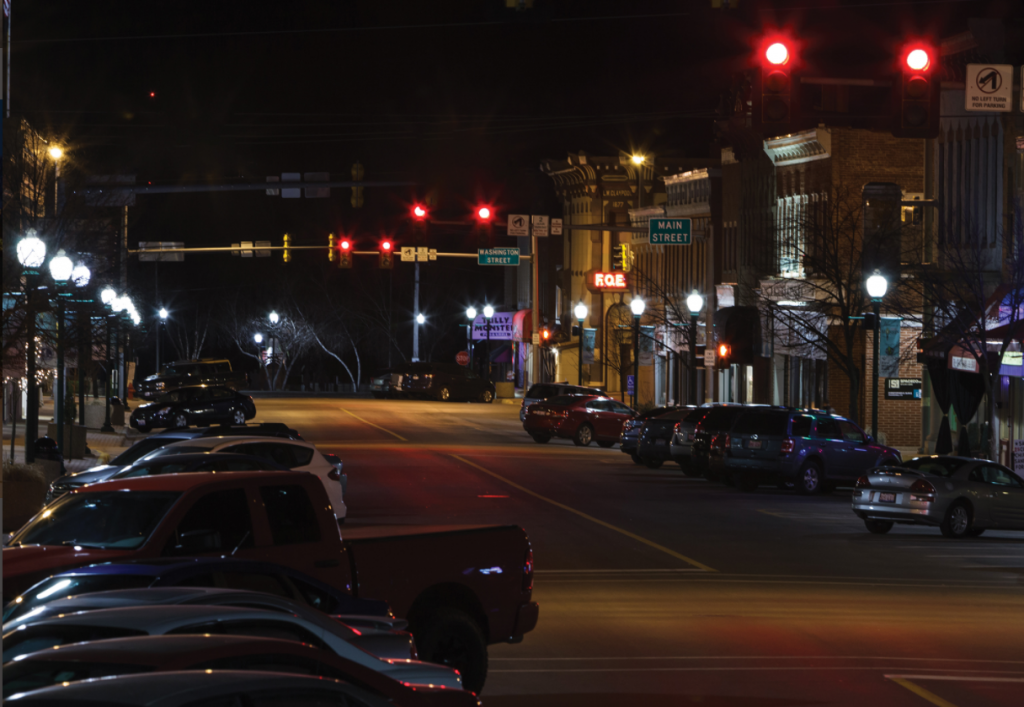
The City of Portland, Oregon upgraded their lighting to Avista LEDs, resulting in a 60% decrease in energy costs.
City managers face several challenges when selecting pedestrian lighting.
These complex projects require a level of collaboration between the city manager and lighting providers to ensure various benefits, such as reduced energy consumption and expense, less maintenance and enhanced color rendering, are realized.
In fact, there are seven important items that should be considered, according to industry experts Lisa Elbert, P.E., who is a signals and lighting engineer with the City of Portland, and Jason Strano, C.E.M., who is an energy sales manager at leading lighting agency Reflex Lighting in Wethersfield, Connecticut.
- Don’t Neglect the Specs. Because fixture performance is key, “spec out every detail and everything you want,” advised Elbert, who thoroughly reviewed and verified Illuminating Engineering Society-specified “LM-79” and “LM-80” electrical and photometric measurements of life and performance on the LED products it evaluated, how the lighting performed using AGI, a simulation tool used for designing lighting projects, and how the lighting actually looked to the eye on Portland’s streets and sidewalks, compared to the city’s previous high-pressure sodium technology. According to Elbert, failure to do this can result in regrets or unwelcome surprises later. (Elbert oversaw the upgrade of Portland’s 6,100 century-old single and twin ornamental decorative fixtures to Amerlux’s Avista LED light engine.)
- Don’t Pass on Due Diligence. Strano agreed that there’s no substitute for a comprehensive due diligence process up-front. “Dismantle a fixture, get the right application or base plate and install it to see how everything works,” he said. “A few hours spent in the beginning taking the proper measurements will make the rest of the job so much easier. Also, allow others to see the new lighting and encourage their feedback before moving forward.”
- Don’t Go Too Big Too Soon. Based on her own hard experience in Portland, Elbert recommends that city managers test streetlighting products on a small scale before proceeding to change every streetlight targeted for upgrade. “On an early LED project we did years ago, we installed 400 lights and within a year suffered a 50 percent failure rate,” she said. “The project had involved a custom fixture incorporating controls that we had made for us and it was untested. When they started failing, there were so many variables involved that we didn’t know whether it was the lighting or controls causing the malfunction. Because ‘too much too soon’ on an untested fixture can be a scary thing, we stick with known, tested products and test them on a smaller scale first, being sure to elicit some feedback before we proceed to a larger installation area.”
- Don’t Fail to Communicate. In addition to anticipating as much as you can on a project, Strano confirmed that good communication is key. “Be as clear about your expectations as possible,” he advised. “If you’re doing a retrofit and you want all of the fixture glass wiped down, for example, be sure to tell the lighting rep, distributor, and/or contractor so that you get exactly what you want.”
- Don’t Forget About the Trees. While Portland and many cities and towns treasure the trees that line their streets, Elbert learned first-hand that those very trees can become obstacles that block light and impair the performance that’s required and expected from streetlighting fixtures. For that reason, Elbert suggests a close review of trees and their distance from streetlights. “We recommend 25 feet of space between lights and trees—less than that triggers a closer review of the tree species,” she said. “Lighting can be as close as 12 feet from a tree if it’s a narrow/columnar tree variety, but a 20+-foot distance between trees and streetlights is advised to ensure that the lighting can operate most effectively and meet its potential.”
- Don’t Ignore the Maintenance Aspect. As part of a comprehensive evaluation process up-front, don’t forget to consider the voice of the contractor or maintenance crew. “Before you select a streetlighting fixture, be sure to review it with the people who will be maintaining it once it’s installed,” Elbert recommended. “The maintenance team sees an entirely different product than we do. While we’re focused on a fixture’s performance, they see what’s involved in terms of the tools and trucks they’ll need to install or repair it. You have to think about what will make a good/easy installation process for the team when selecting a fixture,” she said. “That’s an important cost in the process that can often be forgotten.”
- Don’t Fall for a Fly-by-Night. Strano can’t stress enough the importance of working with a trusted lighting manufacturer who’s vested in the industry. “You want to seek out a product made by a company with history and roots in the lighting industry,” he said. “If you’re going for least cost and you don’t know where the product is manufactured or the company has only been in business for a short time and doesn’t have a known track record, you’re setting yourself up for potential problems. You want to work with a solid manufacturer and/or lighting rep agency with experienced people and all of the resources in place to stand by the product and help you work through any questions or concerns you may have.” Strano added that it’s especially important to make a wise investment up-front given the fact that many streetlighting upgrades are public projects that are funded by taxpayer dollars. (According to the U.S. Department of Energy, streetlighting nationwide accounts for $2-3 billion in annual energy costs alone.)
For more information on Amerlux’s Avista LED light engine, visit http://avista.amerlux.com/.
Want more?